Quality
We are committed to providing customers with highest possible level of quality. In order to achieve this, we are continually improving the processes, products and services meeting and exceeding customer satisfaction at all times.
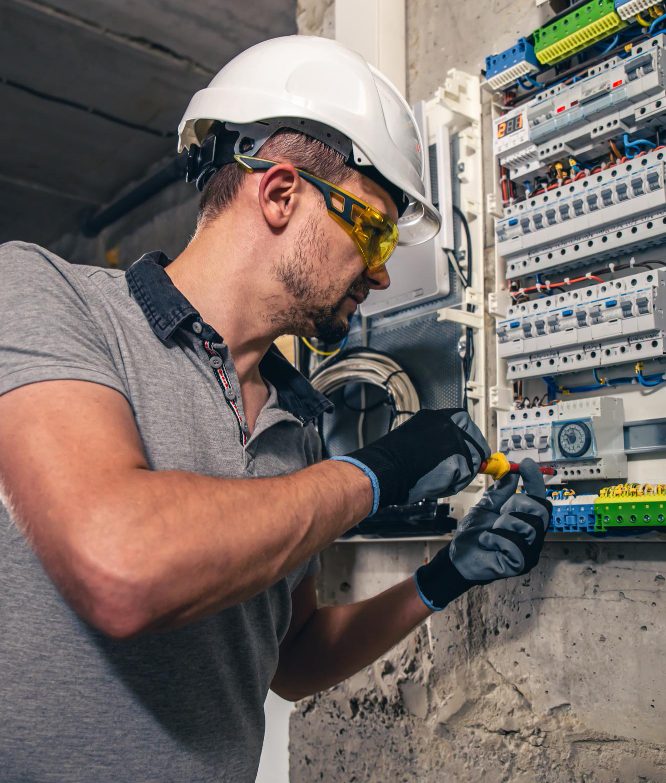
An ISO 9001:2015 Certified Company
All elements of Delta Interconnect operations have been infused with the company’s quality philosophy of a collaborative effort to surpass client expectations.
This quality culture ensures that you and our workforce receive the best possible service and satisfaction. With a special emphasis on your wants and objectives, we create and deliver products that enable optimal functioning.
From idea to finished product, Delta Interconnect’s design process begins with a thorough analysis and an understanding of system requirements. Before we assemble the components, test the components, and certify the subsystem, we go through a functional and physical deconstruction process. The system is taken through a final system test before it is ready for dispatch.
To ensure consistent Quality, we continue to emphasize and invest in our quality processes in the following ways:
- Supplier Quality Management
- Incoming Material Control
- In-process Inspection and Testing
- Sampling procedures followed
- Process Capability Verification
- Quality Auditing
- Defective Material Control
- Calibration of tools and equipment's
- Operator Certification and Training Program
- Testing to Customer Requirements
Plan
Do
Check
Act
A contract manufacturer should be both accommodating and flexible as your needs evolve.
At Delta Interconnect, we realise that you have great business ambitions, but you also have a budget and a timeline to meet. That is why, at every step of the design and production process, we foster efficiency and quality. We empower businesses like yours to innovate and create products that deliver.
The team at Delta Interconnect includes quality professionals specializing in industrial products. With wide product knowledge, industry-specific training and hands-on experience, we provide solutions that help reduce cost and ensure the quality and timely delivery of your requirements.
Design Support
Our experienced design and engineering team and extensive resources can help with technical recommendations, component sourcing and design
Procurement
Our materials team sources components and raw materials worldwide to ensure the best possible combination of pricing, quality and performance, and manages the supply chain so you don’t have to.
Manufacturing
Our primary service offering comes from the high quality manufacturing that takes place on our production floor to maximize the efficiency of our processes.
QA & Testing
As we offer so many different processes, our quality assurance and testing capabilities have to be rigorous. As with our production, we have invested extensively in the personnel and machinery to make sure that we can fulfill our central promiseof high-quality production.
Logistics
Our service does not finish when your product has been successfully manufactured. Rather, we work with our customers to make sure we can find the best possible way to ship your products to you based on cost, lead time and convenience.

For more information, please contact us via Phone or Email
-
Make a call
-
Send us an e-mail